Chemical Safety
Chemical Safety
Chemical Safety is achieved by undertaking all activities involving chemicals in such a way as to ensure the safety of human health and the environment. It covers all chemicals, natural and manufactured, and the full range of exposure situations from the natural presence of chemicals in the environment to their extraction or synthesis, industrial production, transport use and disposal. Chemical safety has many scientific and technical components. Among these are toxicology, ecotoxicology and the process of chemical risk assessment which requires a detailed knowledge of exposure and of biological effects.
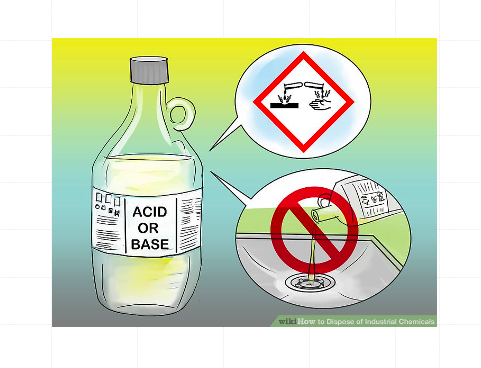
Chemical hazard: is a (non-biological) substance that has the potential to cause harm to life or health. Chemicals are widely used in the home and in many other places. Exposure to chemicals can cause acute or long-term detrimental health effects. There are many types of hazardous chemicals, including neurotoxins, immune agents, dermatologic agents, carcinogens, reproductive toxins, systemic toxins, asthmagens, pneumoconiotic agents, and sensitizers. In the workplace, exposure to chemical hazards is a type of occupational hazard.
Types of chemical Hazard:
- Physical
- Health
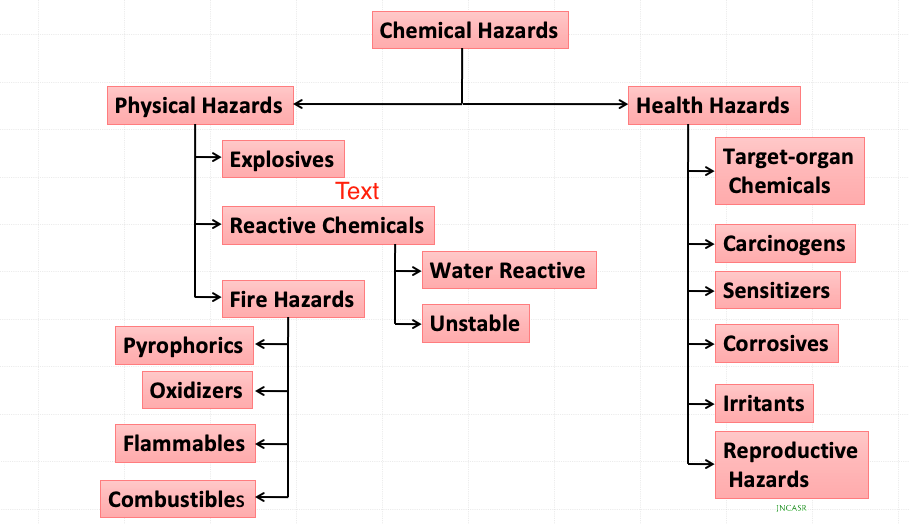
Chemical Exposure
The most common exposure route to chemicals in the work environment is through inhalation. Gas, vapour, mist, dust, fumes, and smoke can all be inhaled. Chemicals may be ingested when food or drink is contaminated by unwashed hands or from clothing or poor handling practices. Chemical exposure to the skin is a common workplace injury and may also occur in domestic situations with chemicals such as bleach or drain-cleaners. The exposure of chemicals to the skin most often results in local irritation to the exposed area. In some exposures, the chemical will be absorbed through the skin and will result in poisoning. The eyes have a strong sensitivity to chemicals and are consequently an area of high concern for chemical exposure. Chemical exposure to the eyes results in irritation and may result in burns and vision loss.
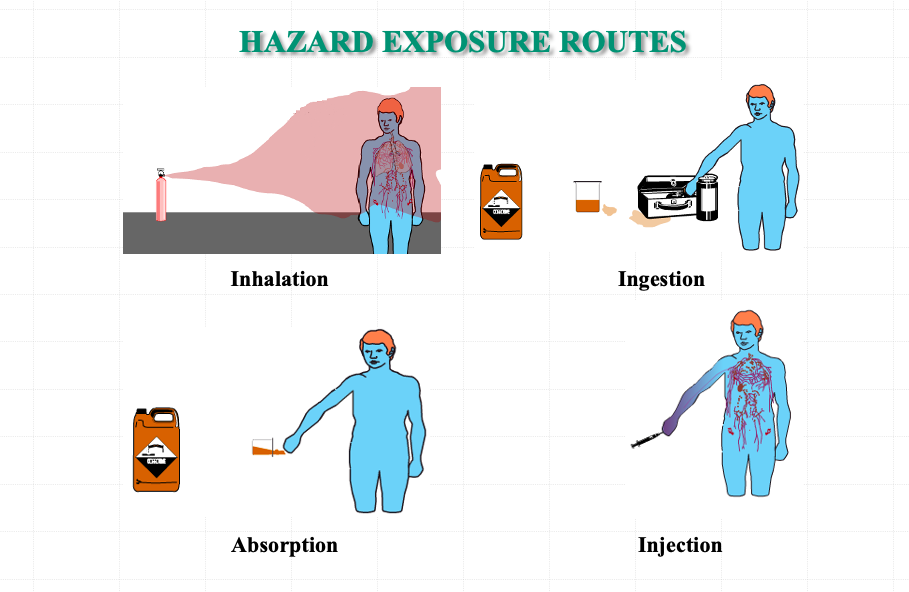
Chemical hazard identification
Principal investigators and lab safety incharges are responsible for verifying if any chemicals or reagents are considered a hazardous chemical. A hazardous chemical means any chemical which is classified as a physical hazard or a health hazard, a simple asphyxiant, combustible dust, pyrophoric gas, or a hazard not otherwise classified in accordance with the Hazard Communication Standard). The Hazard Communication Standard is now aligned with the Global Harmonized System of Classification and Labeling of Chemicals (GHS). GHS provides a common and coherent approach to classifying materials and communicating hazard information through labels and safety data sheets.
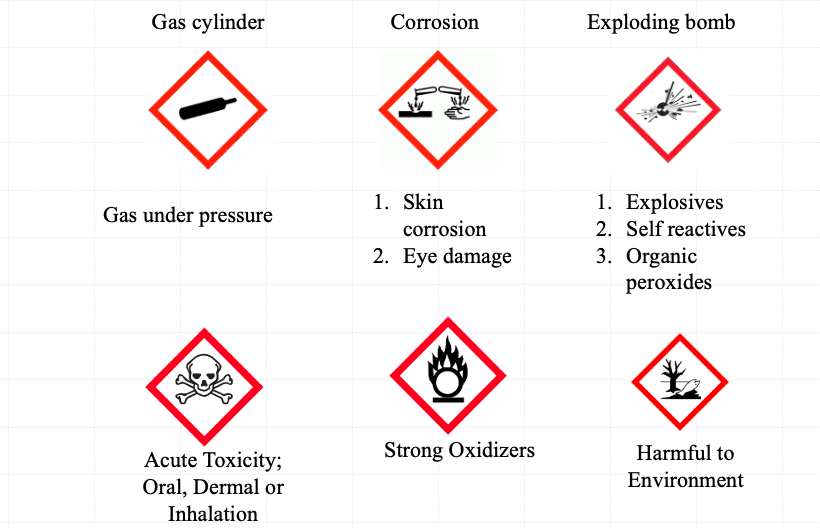
Labels for the chemicals
The purpose of container labelling is to provide an immediate warning to employees of the hazards that they may be exposed to and using chemical identity. Labelling of containers of hazardous chemicals is an essential element of the hazard communication.
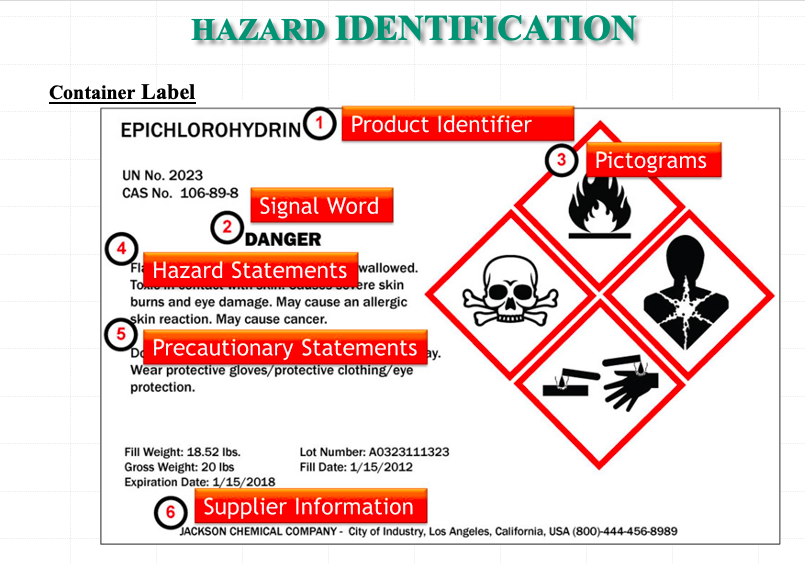
Hazard evaluation
Before beginning the hazard evaluation and risk assessment process, a researcher must define the scope of work. What are the tasks that must be evaluated? A well-defined scope of work is a key starting point for all steps in the risk assessment and hazard analysis.
The next step after identifying the scope of work is to identify the hazard. A HAZARD IS A POTENTIAL FOR HARM. Hazards can be identified as an agent, condition, or activity that has the potential to cause injury, illness, loss of property, or damage to the environment
Hazard controls
Controlling Chemical Exposure Chemical exposures occur via four primary routes:
- Inhalation;
- Ingestion;
- Absorption (through skin, eyes, or mucus membranes);
- Injection (skin being punctured or update through an open wound).
When evaluating the risks associated with specific hazards, the results of this evaluation should guide the researcher in the selection of risk management techniques including elimination, substitution, engineering controls, administrative controls, and personal protective equipment. This is known as the Hierarchy of Controls.
protective equipment. This is known as the Hierarchy of Controls.
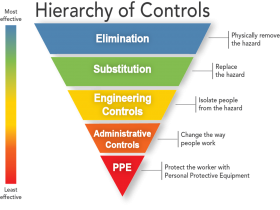
Elimination and Substitution
The most preferred method of controlling risk is to eliminate the hazard altogether. In most cases, elimination is not feasible and when possible, substitution is the best approach to hazard mitigation. When possible, substitute less hazardous agents in place of their more hazardous counterparts. This also applies to conditions and activities.
Engineering Controls
Engineering controls consist of a variety of methods for minimizing hazards, including process control, enclosure and isolation, and ventilation.
- Process controls involve changing the way that a job activity is performed to reduce risk. Examples of this include using wet methods when drilling or grinding or using temperature controls to minimize vapor generation.
- Enclosure and isolation are targeted at keeping the chemical in and the researcher out, or visa versa. Glove boxes are a good example of enclosure and isolation. Interlock systems for lasers and machinery are other good examples of isolating processes.
- The most common method for ventilation in research laboratories is localized exhaust systems. Fume hoods, snorkels, and other ventilation systems are the some of the examples of the same.
Administrative Controls
Administrative controls are controls which alter the way work is performed. They may consist of policies, training, standard operating procedures/guidelines, personal hygiene practices, work scheduling, etc. These controls are meant to minimize the exposure to the hazard and should only be used when the exposure cannot be completely mitigated through elimination/substitution or engineering controls.
Personal Protective Equipment (PPE)
PPE should always be used as a last line of defense and is an acceptable control method when engineering or administrative controls cannot provide sufficient protection. PPE may also be used on a temporary basis while engineering controls are being developed.
First Aid
- In case of emergency, it is recommended to understand first aid procedures in order to minimize any damage. Different types of chemicals can cause a variety of damage. Most sources agree that it is best to rinse any contacted skin or eye with water immediately. Currently, there is insufficient evidence of how long the rinsing should be done, as the degree of impacts will vary for substances such as corrosive chemicals. However, the recommended flush time is as follows:
- 5 minutes - non- to mild irritants
- 15 minutes - moderate to severe irritants and chemicals that cause acute toxicity
- 30 minutes - most corrosives
- 60 minutes - strong alkalis such as sodium, potassium or calcium hydroxide
- Transporting the affected person to a health care facility may be important, depending on condition. In the case that the victim needs to be transported before the recommended flush time, then flushing should be done during the transportation process. Some chemical manufacturers may state the specific type of cleansing agent that is recommended
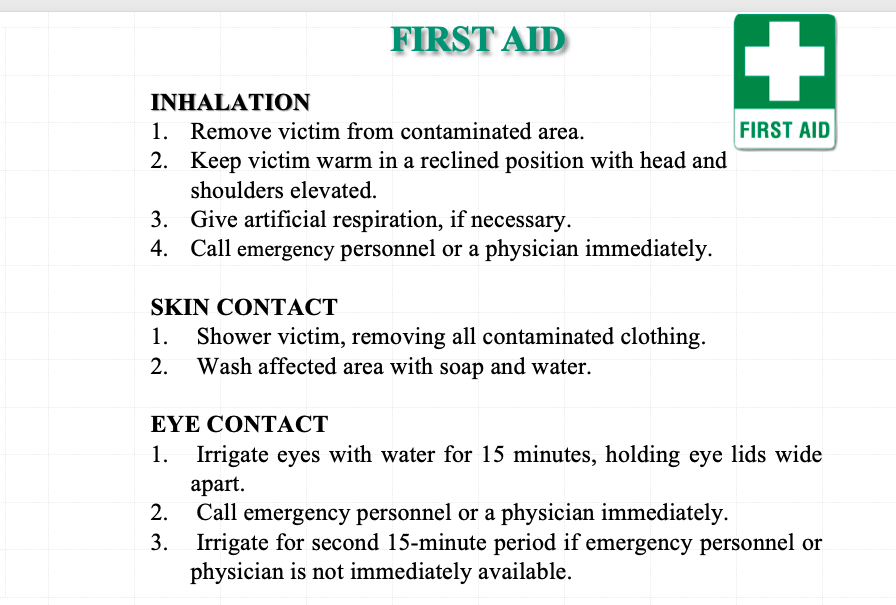
If you need more assistance in chemical safety, please email to jncasr_safety@jncasr.ac.in or can call to +91-8022082710
- Back to previous page
- |
-
Page last updated date:02-06-2025 05:46 PM